در این مقاله به معرفی لوله پلی اتیلن و همچنین نحوه تولید لوله پلی اتیلن خواهیم پرداخت. جنس مواد اولیه ای که در تولید لوله پلی اتیلن استفاده خواهد شد، در کیفیت این محصول اثر مستقیم دارد. چرا که دیده شده لوله را از زیر خاک درآورده و در کوری ذوب می کنند و دوباره بصورت خمیر درآمده و به لوله جدید تبدیل می کنند.
مراحل تولید لوله پلی اتیلن شامل چند بخش مهم و بهم وابسته است که این فرآیندها را به ترتیب معرفی و سپس توضیح خواهیم داد.
- دستگاه نگهدارنده و مکنده مواد اولیه پلی اتیلنی ( گرانول)
- دستگاه شکل دهنده لوله یا همان اکسترودر (Extruder )
- دستگاه کشنده لوله به بیرون
- محفظه خنک کننده لوله تولید شده
- دستگاه لیبل زن
- تیغه برنده شاخه
مرحله اول ( مخزن مکنده پلی اتیلن یا گرانول )
در این مرحله ابتدا مواد اولیه خریداری شده را به داخل دستگاه فشرده کننده اکسترودر از طریف قیف تعبیه شده در ورودی ریخته میشود.
مواد اولیه پس از خشک شدن وارد اکسترودر میشود. جذب احتمالی رطوبت توسط پلیمرها باعث افت ویژگیهای مکانیکی، ظهور حباب و لکه های سطحی در آن میگردد پس باید قبل از ورود مواد به اکسترودر، رطوبت از مواد خارج گردد. گرانولها به طور پیوسته توسط خشک کن های هوای داغ خشک شده و برای انتقال به اکسترودر آماده میشوند.
مرحله دوم ( مخزن اکسترودر )
نقطه ابتدایی تولید لوله همین بخش میباشد که فرآیند تولید لوله پلی اتیلن را آغاز میکند. در ابتدا بایستی گرما به داخل اکسترودر بهمراه فشار توسط ماردون انتقال یابد که وقتی به حالت شکلپذیر (ذوب درآمد) این فشردگی هم به پلی اتیلن شکل دهد. دمای مورد نیاز برای اکستروژن کردن پلی اتیلن بین ۳۹۲ تا ۴۴۶ درجه فارنهایت (در مقیاس اروپایی) بایستی تنظیم شود تا مواد به حالت خمیری در بیاید.
عملکرد اکسترودر در سه بخش مهم صورت پذیر است که در زیر به آنها اشاره کرده ایم:
-
- منطقه یا بخش تغذیه
- ناحیه فشردگی یا کمپکت شدن مواد
- ناحیه سنجش یا آزمون سایز لوله مدنظر
الف) ناحیه تغذیه یا Material injection area
عملکرد این ناحیه بدین صورت است که علاوه بر وجود گرما در اسکترودر ، مواد پلی اتیلن تزریق شده نیز به جلو حرکت کرده و وارد منطقه فشردگی می شود .در این ناحیه عمق تیغه های ماردون بیشتر از دو ناحیه دیگر است و طراحی آن به گونه ای است که با توجه به طبیعت پلاستیک و خواص اصطکاکی آن نسبت به ماردون و محفظه، اکسترودر بتواند تغذیه متعادلی داشته باشد.
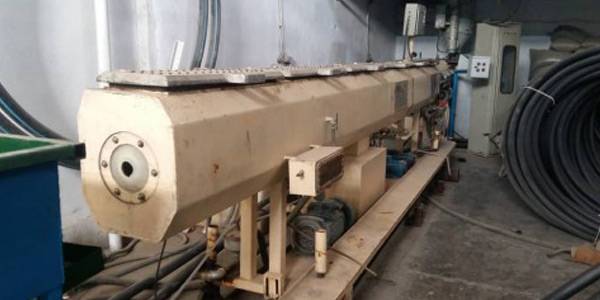
نحوه تولید لوله پلی اتیلن
نحوه تولید لوله پلی اتیلن فشار قوی
ب) قسمت فشرده سازی مواد یا Material compression part
وقتی عمق تیغههای ماردون کاهش پیدا کند سبب متراکم شدن مواد موجود در داخل ماردون و فشرده شدن ماده خمیری می گردد. بدین صورت که در این ناحیه ضخامت پلی اتیلن ذوب شده کاهش یافته و انتقال حرارت آن با دیواره سیلندر بهتر صورت می گیرد. وقتی فشردگی در این ناحیه صورت می گیرد سبب بازگشت هوای حبس شده در داخل ماردون و بازگشت آن به ابتدای اکسترودر می شود. (به همین دلیل سوپاپ اطمینان نیز در روی اکسترودر تعبیه شده تا در مواقع اضطراری هوای حبس شده بیش از اندازه در آن قسمت نمانده و خارج گردد)
ج) ناحیه سنجش فشردگی یا Compression section
در این بخش عمق تیغه اسکترودر در بخش ماردون کاهش یافته ولی به اندازه سایز طراحی شده مانده و ثابت میماند. به همین دلیل مواد مذاب به صورت همگون و یکنواخت در می آید به طوری که با آهنگ ثابتی در درجه حرارت و فشار یکسان و ثابت، به قالب یا حدیده وارد میشود.
چند نکته مهم در خصوص اکسترودر:
اکستروژن یکی از روش های شکل دهی است که برای کاهش ضخامت یا سطح مقطح مواد به کار میرود. این عملیات با استفاده از دستگاه اکسترودر صورت میپذیرد که به انواع اکسترودر تک ماردونه و دو ماردونه تقسیم میشود.
امروزه برای کنترل دقیق خروجی اکسترودر و سرعت تولید به صورت بهینه، سیستمهای کنترل اتوماتیک گراویمترک توسعه یافتهاند که با تعدیل نوسانات حاصل از تغییر در شرایط کاری، تاحد ممکن موجب ثبات خصوصیات محصول نهایی میگردند.
همیشه بعد از تولید یک متراژ معین از لوله پلی اتیلن (بستگی به دستورالعمل نوشته شده در کاتالوگ دستگاه دارد) بایستی دستگاه مذکور تمیزکاری و سرویس گردد. این کار هرچند ساده بنظر می رسد ولی در اصل عمر اقتصادی دستگاه را بالا میبرد.
مرحله سوم (بخش مکش مواد بوسیله ماردون)
ماردون موجود در دستگاه اکسترودر دارایی تیغههایی خمیده هست که هنگام کار کردن مواد را بصورت دورانی به جلو حرکت میدهند و در این میان فشردهتر و به طرف خروجی اکسترودر حرکت میکند.
مرحله چهارم (قالب گیری و شکل دهی به پلی اتیلن)
در خروجی اکسترودر مواد خمیری همگن و همسان جهت شکل یافتن به سایز مورد نیاز از قالب نصب شده در دهانه این دستگاه به بیرون میآیند (به این قسمت نصب شده سر دهنده یا کلگی دهانه می گویند).
مرحله پنجم (تثبیت سایز مورد نظر لوله پلی اتیلن بوسیله تانک خلا خنک کن)
وقتی سایز مورد نظر لوله پلی اتیلن از اکسترودر خارج شد بایستی شکل خود را حفظ کند که در اینجا از محفظه تانک خلا به همراه آب (جهت خنک سازی و تثبیت شکل و سایز لوله مورد استفاده است) عبور داده می شود و نهایتا سایز لوله مورد نظر تولید میگردد.
مرحله ششم (مارکینگ لوله)
بعد از عمل خنککاری بایستی تولیدکننده برند شرکت خود را به روی لوله هک نماید که این عکل هم توسط دستگاه لیبل زن صورت میگیرد.
مرحله هفتم (برش شاخه تولید شده)
نهایتا میدانیم شاخه های هر لوله پلی اتیلن بین ۵۰ تا ۷۰ متر متفاوت است. به همین دلیل طبق دستورالعمل و درخواست کارفرما لولههای مورد نظر توسط تیغهها برش داده شده و بصورت شاخهای بستهبندی میشوند.
ناگفته نماید سایزهای کوچکتر میتوانند خم شده و بصورت رول دپو شوند. هر چند بدین صورت باشد، حمل و انتقال به محل پروژه هم آسانتر خواهد بود.
تعریف گرانول PE: گرانول پلی اتیلنی سفید رنگ بوده و مانند دانههای مروارید در سایزهای کوچک میباشد (منظور از واژه PE خلاصه واژه Polyethylene است)